5 technical requirements for rail track?
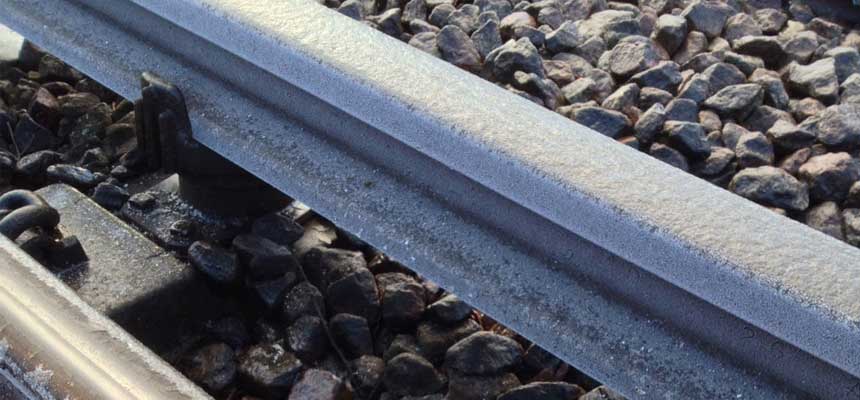
As the basic component of railway track system, rail track keeps the safety, stability and continuous running of railway line. The common standards of rail track on the international market include ASCE, BS, UIC, DIN, JIS, GB and etc. How it is made? There are some properties of rail track can’t be ignored before rail track production.
-
Strength: The rail tracks must ensure that the stresses and deformations do not exceed the specified limits under the effects of wheel load and rail temperature changes. So that requires the sufficient strength, toughness and wear resistance of rail tracks.
-
Roughness: the locomotive relies on the friction between its moving wheels and the top surface of the rail to pull the train forward, which requires the top surface of the rail to be rough, so that sufficient friction between the wheel and the rail is generated. However, for vehicles, too much friction will increase the driving resistance, which in turn requires the smooth rolling surface of rail track. From the view of this contradiction, the rail should still maintain its smooth surface. If necessary, sanding on the rail surface can be used to improve the adhesion between the moving wheel of the locomotive and the rail track.
-
Elasticity: the rail track relies on its own stiffness to resist the elastic bending under the wheel load, but in order to reduce the dynamic impact of the wheel on the rail track, to prevent the loss of the running parts of the rolling stock and the rail track, so the rail is required to have the necessary elasticity.
-
Tenacity: the contact area between the wheel and rail track is small, and the pressure from the wheel is very large. To prevent the rail track from being crushed or worn too fast, the rail should have sufficient hardness. However, too high hardness makes rail easy to be damaged by the impact, and therefore, the rail track is required to have certain tenacity.
-
In addition, the demand for different types of rail tracks should also be considered. Therefore, the rails must be designed reasonably, at low prices, and with complete weight.
In order to meet the above requirements, the material, section shape, weight, strength, toughness and wear resistance should be fully considered when designing and manufacturing the rail track.
Rail track production
Surface quality
-
The rail track should pass the quality test according to specific standard before leaving factory. Because there are countless standards of rail track, we take GB standard as an example, technical requirements as follows:
-
The lateral curvature of the rail track shall not exceed 1 mm per meter and the total curvature shall not exceed 8 mm;
-
The total curvature of the rail in the upper and lower directions shall not exceed 6 mm;
-
The bending of the end of the rail within 0.5m shall not exceed 1.0mm;
-
The rail torsion shall not be bigger than 1/10000 of the total length of rail;
-
Asymmetry of the cross section and vertical section of the rail: the rail bottom shall be less than 2 mm, and the rail head shall be less than 0.6 mm;
-
The rail bottom should not be recessed. The center of rail bottom shall not protrude more than 0.5mm from both sides;
-
The rail surface must be free of cracks, folds and lateral scratches. It is allowed to have knots, indentations, bumps and individual lines up to a depth of 1 mm. The longitudinal scratch depth must not exceed 0.5mm. There shall be no lines on the center of the rail at 1/3, and the depth of other defects shall not exceed 0.5 mm. There shall be no residual pores, delamination, cracks on the rail section and bolt hole surface, and the burrs on the edge shall be removed;
-
The low-power structure shall have no shrinkage cavity residuals, internal cracks, dissimilar metal inclusions, skin turning, delamination and visible inclusions during inspecting. Spot segregation, rimhole, and surfaces inclusions must not exceed the regulations for low power images. Rails must not have white spots.
Rust-proof treatments of rail track and steel plate
-
The surface of the rail is completely bared by sand blasting. Apply two layers of epoxy zinc-rich primer.
-
The top of the rail is not painted, and no paint is applied within 30 cm of the end of each rail.
-
After the base of the press plate is welded to the steel plate, the rust stain on the steel plate is removed, and the surface is coated with two layers of epoxy zinc-rich primer (including the base). The primer is 40 μm thick, and the bottom of the steel plate is not painted. After the primer is dry, the steel plate is fixed on the pre-embedded bolts, and then coated with two layers of vinyl or polyurethane topcoat (including the base), the topcoat is 100 μm thick.
End cropping
End cropping is a key link that is related to the quality of the rail installation. The cutting surface is required to be 90 with the rail. The length error is less than 0.5mm.
Rail welding
Rail bottom welding:
After the rail was placed on the bottom mold, a small steel piece (12 mm × 3 mm × rail bottom width) was placed in the gap at the end and the sides were ground to a 45° bevel. Firstly, the metal should be welded along the side of the small steel sheet.
After the first row is welded, the slag should be removed immediately, and the first pair of separate mode should be placed and welding the second row. During welding, the slag should be removed through the gap between the mold and rail track.
Rail neck and head welding:
When the welding at the bottom of the rail is completed, a separate mode matching the curvature of the rail may be placed, and leave a gap between the separate mode and the rail for flowing slag out. When soldering to the height of the second layer of separate mode, the welder should immediately place the upper and lower layers of the mode and continue welding.
After the welding is completed, the rails should be immediately covered with insulation such as felt. The cooling time is required more than 12h, and the felt and protective pad can be removed when the weld temperature is below 60℃.
The protruding portion of the rail weld joint shall be polished. Polishing can be done when the weld temperature drops to atmospheric temperature. The polishing operation should be carried out slowly and carefully. The top of the weld is particularly important and must be smooth and free of recesses.
Site physical and chemical testing should be performed for each weld.
Check and accept
-
The acceptance of the rail track is carried out at the construction site and is checked one by one;
-
Straighten the rails, and mark in the top, middle and tail tops of rail with red paint.
-
The Brinell hardness of the welded joint should be higher than the base metal 20N/mm2, and the neck bending force should be bigger than 120t.